What are Plastic Conveyor Rollers?
- David Fenton
- Jan 17, 2022
- 3 min read
Updated: Sep 12, 2023
Conveyors are mechanical systems that make handling material very easy. You can transport all types of materials from complicated structures materials to bulks in sacks and boxes to powdered materials. Any kind of mass production system has a conveyor as an integral part of it. Depending on the requirement the functionality of the type of conveyors varies. However, their working principle is the same across all types and variations.
Be it gravity-based conveyors used to move objects utilizing gravity or power-driven belt conveyors, bucket conveyors, or roller conveyors, all work with the same principle. The plastic roller-based roller conveyor, popularly known as plastic conveyor rollers is what we are going to discuss in this article. We will try to understand the design, types, and usage of these special types of roller conveyors, among some common systems.
Before delving any further into the subject of plastic conveyor rollers, let’s try to understand the conveyor system. In simple terms, roller conveyors are a type of conveyor belt system that has a set of evenly spaced rotating cylinders (rollers), arranged in the form of a belt.
Over this sequence of rollers, materials can be moved from one destination to another with ease.
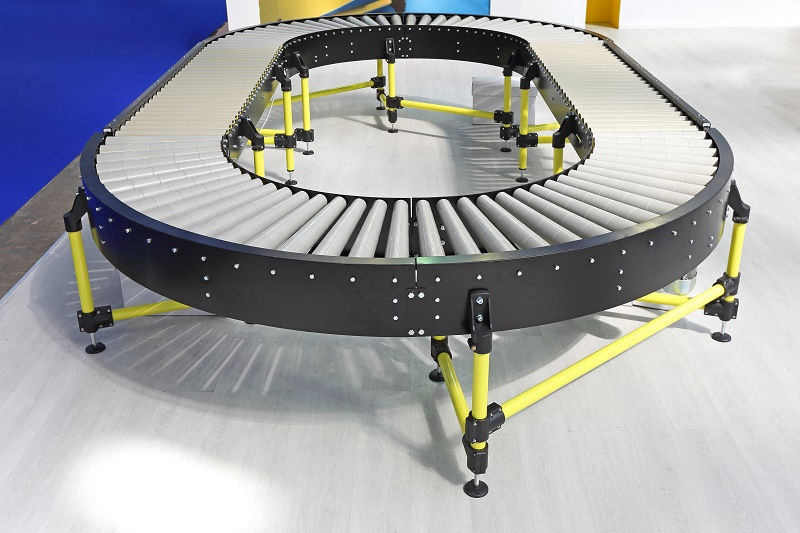
The material is basically skated over this surface made of rollers from one destination to another. The rollers may be made of steel or plastic. The name plastic conveyor rollers comes from the plastic materials that are used in the rollers.
The design of the plastic conveyor rollers is very simplistic. However, the core system concepts have been improved and upgraded several times to keep up with the latest industry trends and requirements. The greatest addition to the conveyor roller system is the introduction of the drive. In this system, the Rollers are connected to a motor through a belt chain or shaft. This induces more controllability of the system. The primary functionality that is seen in the plastic conveyor rollers is that the materials move at a predefined speed along the pathway on the surface of the conveyor. One advantage of the roller-based conveyor system is that it can go bi-directional. As a result, the efficacy of the conveyor increases manyfold. The roller frame is one of the most important components of the conveyor. They basically define the pathway for the conveyor. Generally, the frame is made of aluminum or steel. However, depending on the type of material to be transported and also the weight of the material, and the area where the conveyor is to be installed, the roller frame may be made of other materials. One of the major advantages of plastic conveyor rollers is that they have higher friction, enabling the movement of the material in a much controlled manner. The size of the rollers also has an important role to play in the operation of the conveyor. Depending on the probable size, dimension, and weight of the material that will be transported, the size of the rollers may vary. Next comes the distance between each roller; based on the size of the materials that will be transported, the rollers are so placed that at any point of time during the transport, three rollers will always be touching the material.
To Conclude
Not to forget, that the loading and the accumulation mechanism of the conveyor is an important feature to know. The question is; How Heavy is the item that would be transferred? Also, questions like ’Are the materials that will be transported fragile’ and others impact the type of rollers to choose.
Finally, after all this discussion, it is now a bit clear about the plastic conveyor rollers and their functionalities. Expectedly it is clear about the workings of the conveyor rollers.